By Betsy Conroy
The factory is changing. Industrial cabling infrastructure has migrated from traditional proprietary protocols to open interoperable Ethernet for transmitting information across supervisory systems and to upper level planning and management systems. Fueled by emerging Industrial Internet of Things (IIoT) technologies and Industry 4.0 , the adoption of Ethernet-based communications is now moving deeper into the industrial environment to replace fieldbus systems and enable an all-Ethernet ecosystem. A recent report from HMS Networks estimates that Industrial Ethernet applications like EtherCat, Ethernet/IP, and Profinet now account for more than 65% of new installed nodes in factory automation and continue to gain market share, while legacy fieldbuses show decline year over year. This migration to Ethernet, along with trends in modularization, miniaturization, and remote power all impact industrial cabling and connectivity.
Not your standard Ethernet
In comparison to the commercial office space, Industrial Ethernet cabling requires ruggedized components to handle the harsh environment of the factory floor. TIA and ISO/IEC cabling standards for industrial premises use MICE (i.e., mechanical, ingress, climatic, and electromagnetic) tables for classifying the severity of the deployment environment, where Level 1 is a commercial environment, Level 2 is light industrial, and Level 3 is the most severe industrial environment.MICE tables are used to ensure that cabling and connectivity deployed in these environments will function properly. For example, if the environment is an I2 or I3 (i.e., Level 2 or Level 3 ingress rating), connectivity may require ingress protection. The use of industrial-grade IP67-rated RJ45 connectors is common throughout the factory, while MICE1 environments typically correspond to IP20-rated connectivity. Automation environments subject to vibration also often use M-series locking thread connectors that come in a variety of types and sizes, with the most common being the M12 and M8 that terminate to twisted-pair industrial cabling.
For the cables themselves, cost-effective polyvinyl chloride (PVC) jacketing used for commercial-grade cables in MICE1 environments may not stand up to temperature, chemicals, abrasions, flexing, and other harsh elements in MICE2 and MICE3 environments. Industrial cables typically require jacketing materials like fluorinated ethylene polypropylene (FEP), thermoplastic elastomer (TPE), or thermoplastic polyurethane (TPU or TMPU) because those materials enable broader operating temperatures, higher tensile strength, greater flexibility, and resistance to chemicals and abrasions. Copper cabling deployed in noisy E2 and E3 industrial environments are shielded to prevent electromagnetic interference (EMI) that can degrade performance.
In addition to environmental considerations, Industrial Ethernet requires different functionality than standard commercial Ethernet that uses Carrier Sense, Multiple Access with Collision Detection (CSMA/CD) to transmit data only when it’s clear to send—meaning the time it takes for data to reach its destination cannot be determined. Industrial automation and control systems cannot tolerate this non-deterministic transmission, which is why IEEE 802.1 time-sensitive networking (TSN) standards that add prioritization and time synchronization behaviors are vital for Industrial Ethernet applications. Additionally, industrial networks commonly require and employ different topologies and requirements to facilitate redundancy and uptime—everything from multidrop bus topology for operating several nodes on a single link, to hybrid star-ring topologies that minimize downtime. Protocols like High-availability Seamless Redundancy (HSR) defined in IEC 62439-3 that sends data packets in both directions simultaneously are deployed for systems that must achieve zero recovery time.
As industrial operations shift to an all-Ethernet approach, operational technology (OT) teams are also faced with an aging workforce and lack of skill. While this is an opportunity for the Ethernet-savvy younger generation to bring their skills to the industrial space, Adnan Ahmed, RCDD, DCDC, RTPM, director of the technical advisory and solutions group for R&M, says, “It’s not easy for those that have only been in the commercial space to just move to industrial. While we can train IT professionals that already understand Ethernet, the criticality of uptime, and cybersecurity, they need safety training and education surrounding the standards, MICE environments, and the intricacies of industrial Ethernet. But at the end of the day, a termination is a termination and there is a workforce shortage.”
It's a 4.0 thing
Supervisory control and data acquisition (SCADA) systems have long relied on Industrial Ethernet to gather data from control-level programmable logic controllers (PLCs) and terminals throughout the factory. Data from these systems transmit to manufacturing execution systems (MES) and enterprise resource planning (ERP) platforms—either on-premises or in the cloud—that give supervisors, plant managers, and C-level executives plant-wide visibility of purchasing, inventory, production, and supply chain activities for effective forecasting and budgeting.
“You can’t talk about Industry 4.0 without talking about infrastructure,” says Sylvia Feng, global manager digital automation consulting for Belden. “We need to build the central nervous system to reliably collect and send all that data in real-time from devices to servers and the cloud. Using multiple protocols is just not sustainable—whether it’s data from a temperature sensor or an ERP system, we need unified protocols to be able to put all the data in one bucket.”
As Industry 4.0 comes to fruition and an all-Ethernet ecosystem emerges throughout industrial networks, facilities are also breaking away from rigid infrastructure via modularization that enables faster, more-versatile deployments and reconfigurations. As machines become more complex and smaller IIoT devices connect, there is also the need to address space limitations through miniaturization and reduced materials. These trends aim to optimize operational efficiency, cost, and sustainability—all objectives of Industry 4.0. They also drive innovation.
“It’s important to look at total cost of ownership. Industrial and manufacturing entities want to collect data from devices in environments with limited space,” says Belden’s Feng. “We therefore need infrastructure to be lighter and smaller. The weight of the cabling alone is the third heaviest component in a modern-day car, and there is value in any size reduction that still guarantees signal transmission. The same is true in the automation world.”
In response to the need for modular, smaller components, HARTING introduced its ix Industrial connector for Ethernet that offers Category 6A performance with a 70% smaller design than conventional RJ45 connectors, as well as miniaturized M8 and M12 connectors. HARTING’s complete line of angled and push-pull ix Industrial, RJ45, fiber, and M-series connectors also facilitate connections and disconnections in tight industrial spaces.
“From a mechanical point of view, there is a lot of activity surrounding miniaturization and push-pull connectivity for easier operation, but it’s also about reducing materials and looking to non-hazardous alternatives. We’re refining our own internal manufacturing process to develop new products under the aspect of both performance and sustainability,” says Rainer Schmidt, business development manager for industrial cabling at HARTING. Schmidt also points to remote powering via technologies like Power over Data Line (PoDL) and Power over Ethernet (PoE) that further improve sustainability by eliminating the need to run separate AC power to devices and improving overall energy efficiency.Testing Industrial Ethernet is also evolving. “There is little history of full compliance testing of the installed cable plant against the requirements of cabling standards in the industrial space where components are highly reliable and designed to operate at low data rates. Testing has primarily been achieved via continuity testing or at the application layer during commissioning via packet analysis or by connecting systems together to verify that they work,” says James Withey, research and development engineer for Fluke Networks. “But as Industrial Ethernet continues to evolve and proliferate, and we move to increased data rates, lengths, and frequencies, it becomes more important to test during installation.” Fluke’s DSX CableAnalyzer supports RJ45, M8, M12, and HARTING’s ix Industrial connectors. The tester also includes channel test parameters for several Industrial Ethernet applications based on end-to-end limits in ISO 11801-9902 standards that include testing end connectors, which the company recommends for point-to-point links common in industrial environments.
The SPE game changer
Replacing proprietary fieldbus systems like DeviceNet, Profibus, CAN (Controller Area Network), and ASI (Actuator Sensor Interface) at the field/IO level was a key driver for the development of single-pair Ethernet (SPE) standards like IEEE 802.3bw 100Base-T1 and 802.3bp 1000Base-T1 for automotive applications and the latest IEEE 802.3cg 10-Mbit/sec standards. Addressing both commercial and industrial environments, 802.3cg variants include 10Base-T1L for longer-reach point-to-point communications up to 1000 meters and 10Base-T1S for short-reach multidrop connections of at least 8 nodes up to 25 meters. These applications also support remote powering via PoDL at 12, 24 or 48V DC in engineered networks or SPE PoE (SPoE) for 24V or 55V DC in classified networks.According to Andrea Briggs, product manager for field wiring at Weidmüller, extending Ethernet to the field/IO level was previously cost-prohibitive and complicated because the majority of these devices don’t need the multigigabit speeds supported by larger, heavy four-pair category cables. Depending on the industrial site, some devices also need a longer reach than the 100 meters allowed by category cable, while others require bus (or multidrop) topologies. “Single-pair Ethernet is the key to cost-effectively bring Ethernet to the sensor level for more efficient control and increased levels of automation,” she says. “With only one pair of wires able to provide the same transfer rates along with remote power, single-pair Ethernet enables less material, weight, and space for easier, more sustainable deployment in industrial spaces.”
Following the release of 802.3cg, IEC developed a series of 63171 connector standards and 61156 cabling standards for both commercial (MICE1) and industrial (MICE2 and MICE3) applications, with MICE1 targeted primarily to building automation systems in commercial smart building environments. SPE was then incorporated into the ISO/IEC 11801 series of cabling infrastructure, and earlier this year, TIA released the ANSI/TIA-568.5 SPE component standard in alignment with ISO/IEC. The TR-42.9 industrial cabling work group is now developing ANSI/TIA-568.7 for balanced single twisted-pair for industrial premises, and SPE will be incorporated into the TIA-1005 industrial cabling standard. Both ISO/IEC and TIA cabling standards for SPE recommend the IEC 63171-5 T1 connector from HARTING for MICE2 and MICE3 environments and the IEC 63171-1 copper LC connector from CommScope for MICE1 environments, but also permit other IEC-approved SPE connectors.
While the SPE market is still in its initial stages and will require adoption by active equipment and device manufacturers before ramping up, several cabling and connectivity manufacturers have already developed solutions to support the technology. With HARTING’s T1 connector approved and recommended by standards, the company is developing solutions across their portfolio that includes IP67 ratings and well-known M8 and M12 circular housings. TE Connectivity is cooperating with HARTING to develop T1-based solutions, and they have also developed a hybrid SPE system for simultaneous Ethernet data and power supply through an M12 in accordance with IEC 63171-7. R&M is developing end-to-end SPE systems for MICE1, MICE2, and MICE3 environments based on their MSP connector in accordance with IEC 63171-2 and its compatible Phoenix Contact SPE ONEPAIR connector in accordance with IEC 63171—5, which can be used in standardized M8 housing. Weidmüller is also actively developing SPE solutions based on the compatible MSP and ONEPAIR connector, including a field-attachable connector and through-cabinet SPE coupler for connecting the MSP (MICE1) to the M8 ONEPAIR (MICE2 and MICE3).
For MICE2 and MICE3 environments, Belden now offers an SPE version of their industrial DataTuff cables with shielded and industrial jacketing options. To collect digital information from the field/IO level in the industrial space while the market waits for SPE-enabled equipment and devices, Belden’s line of I/O solutions for industrial connectivity includes IO-Link Master and I/O Hubs that transmits digital signals from connected field devices to controllers using Industrial Ethernet protocols. Several cabling and connectivity vendors associated with the commercial space are also developing SPE solutions for building automation systems in MICE1 environments, including Siemon, CommScope, Panduit, Belden, R&M, and others.
More to come
Several SPE alliances and consortiums formed over the past few years, including the TIA Single-Pair Ethernet Consortium (SPEC) comprising several commercial cabling and testing equipment manufacturers. Similarly, the Single-Pair Ethernet System Alliance comprises several industrial and building automation device manufacturers, as well as cabling and connectivity vendors that play more in the industrial space. There’s also the Single-Pair Ethernet Partner Network and plenty of SPE subgroups and committees within several other industry associations, with focuses on industrial as well as commercial building automation. Ethernet-APL (Advanced Physical Layer) for harsh processing environments based on the 10Base-T1L standard was also developed by a group of suppliers.“SPE plays a significant role in three big markets—building automation, industrial, and automotive. It’s important that we all work together to share ideas and strive for complementary solutions across standards,” says HARTING’s Schmidt. “Ultimately, there is pressure from the customer base in all these markets—they want scalable systems that are open for the Ethernet applications and components they want to use.”
Work within standards bodies, alliances, and consortiums will lead to more applications and innovations that enable all-Ethernet industrial systems—from field devices all the way to enterprise and cloud-based systems. While SPE adoption by equipment and device manufacturers has been slow, which most attribute to the impact that Covid-19 had on investment in new technologies and the supply chain, the overall Industrial Ethernet market continued to grow throughout the pandemic. A recent report by MarketsandMarkets highlights rapid growth in 2020 for Industrial Ethernet and estimates that will continue over the next four years. The report highlights the demand for interoperable open protocols, advanced automotive technology, and the need for new approaches to production and assembly to meet changing customer demands. Industrial cabling and connectivity vendors will therefore continue developing new solutions in support of Industrial Ethernet.
Betsy Conroy is a freelance writer, editor, and content consultant specializing in business-to-business media and commerce. Cabling Installation & Maintenance commissioned Betsy to write this article.
About the Author
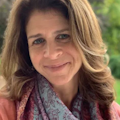
Betsy Conroy
Betsy Conroy has spent the past three decades writing quality technical content and leveraging that content to launch impactful integrated marketing campaigns. She started her career as a technical and promotional writer for medical, security, and environmental corporations. In early 2000, she became an independent freelance writer, editor, and content consultant, focusing primarily on B2B manufacturers and associations in the electrical, networking, and telecommunications industries. Betsy frequently publishes content in a variety of industry publications on behalf of her clients and is also a contributing writer to Smart Buildings Technology Magazine. She was previously a monthly contributing writer to Cabling Installation & Maintenance Magazine and chief editor of BICSI News Magazine for five years where she was instrumental in bringing the publication from a newsletter status to that of a preeminent trade magazine and helping to launch BICSI’s premier publication, ICT Today.